Cost to build prefab house
- TechPrefab
- Mar 16, 2021
- 4 min read
Prefab construction, often time we can refer to off-site construction, is the superstar in the AEC industry and gets a lot of attention from developers, landowners, and even venture capitals. The promise of the technology is attractive — to move partial or entire house construction work in a protected and controlled environment/factory so that it is cheaper and faster to build, greener to the environment. Since the beginning of TechPrefab, I have the fortune to work with many clients and friends on their exciting prefab projects. The experience has tremendously shaped my view on the prefab industry.

Container modules for a student apartment — ready to start the finishes
Before we started the Tech Prefab, Robert, Z.Z., and I spent a fair amount of time trying to understand prefabs’ advantage. Interestedly, many people have different views on what a prefab is and its advantages, but most of these views point to one important factor: Cheap.
So for my first blog of this series, I decided to talk about the $$$ of prefab constructions and how you can save real bucks with these technologies. Disclaimer, all my researches are based on low-rise residential constructions. I will be happy to discuss and exchange ideas if you disagree with my view.
So will prefab save cost? From my projects experiences, the answer is: No, Prefab cannot save you money. In fact, it may cost you more to build one!
First, let’s take a look at a modular company’s offer:
A start-up offers a 1440 SFH house (model layout is set with the limited customization option) for $409,500, which is $284/sqft. Notice the word “starting at”? It may reach $300/sqft or above for an average site (Northern California area).
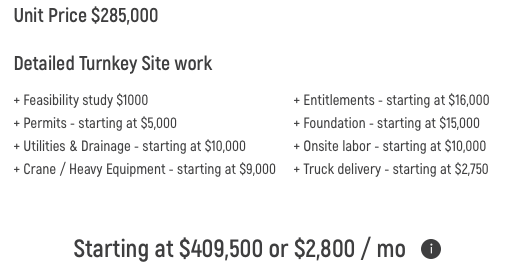
One modular company’s offer
In comparison, a stick build in the same region can build around $260-$310/sqft for a similar size house.
How about SIPs?
A similar situation can be found in houses built with structural insulated panels. The innovation of panelized technology is to build a sandwich wall and roof panel that includes structural elements and insulations, thus saving time and labor cost on-site. The promise is attractive, but in reality, it rarely saves cost — often time it even costs more. A study from the University of Colorado conducted in 2015: “the true cost of SIP” reveals SIP panels’ cost vs. stick framing.

Though many SIP manufacturers market the savings from labor, sometimes, they use the number 50% labor savings. But this is the reality — The labor-saving should really refer to the framing labor savings, which is often 20% or less of the total construction labor cost. Second, The price of the SIP panels per vertical square feet is usually much higher than buying the raw materials off the shelf, for example:
Stick build materials:
7/16" OSB, 4x8: $20.50 per board (link)
5.5" EPS, 4x8: $53.66 (link)
This gives us a roughly $3 sq.ft. (wall surface area)
For SIPs price, it ranges from anywhere between $5.50/sq.ft. (link) to $10/sq.ft (link). Will the cost difference offset by labor-saving? Hardly, and we haven’t even include the shipping cost to move the SIP panels to your site, and the cost for additional logistic management.
There are still a great amount of prefab construction systems!
Yes, correct! In this study from Mckinsey (link), there are many ways to do prefab constructions. Each way has its unique advantages that may solve one or multiple issues. However, so far, along with our researches, most of the prefab construction is either struggled with their pricing or regulations (e.g., a fold and expand house).
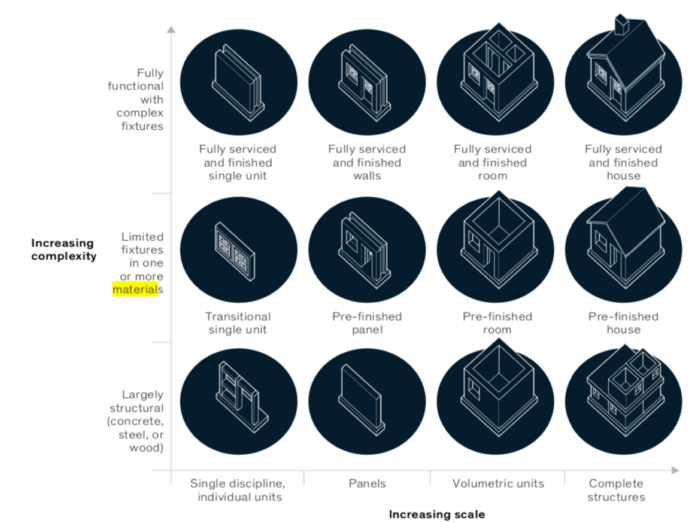
With volumes, these prefab will become much more cheaper!
This is hardly an argument. Let’s compare prefab or modular with the national builders such as NVR.
The national builders typically select a big site, subdivided into 100s lots for sale. On these 100s lots, they provide a limited number of models for customers to configure. Their cost is usually 30%-40% lower than your local custom home builders because of its large quantity and focused labor groups on site (means a dedicated team only works for these 100s lots).

One RyanHome development site
Let’s set aside the constraints of modular / prefab designs. Once these factories or companies get volume, can they really save another 30–40% costs than those national builders? In east coast, it means $50-$60/sq.ft. or Bay area $150/sq.ft, end-to-end (including foundation). Is it possible? I am not sure, but certainly, it won’t happen soon.
Maybe, let’s take a step back and say with volumes, prefab can match the national home builder costs. Building a custom home at national builder’s cost is also extremely attractive to many developers. However, more issues may come from the inspection, construction loan schedules, insurances, and appraisal that could easily ruin your project.
Does it mean Prefab is not worthy?
In contrast, I want everyone to steer away from the cost perspective but focus on Prefab’s value delivery. We have done several prefab projects, from panelized walls to modular. There are two benefits I really enjoyed when working with Prefab.
Forward thinking in construction.
Yes! Plan early, plan thoroughly is one great attribute when working on a prefab project. When working with a manufacturer, you are literally bringing in the manufacturer as part of your design team for incorporating their unique systems.

Preconsruction BIM — LOD350 to LOD400
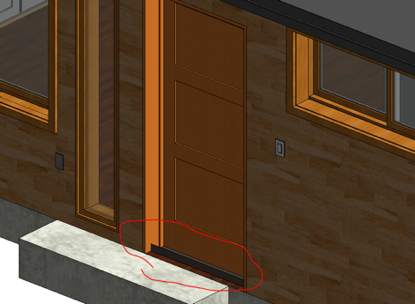
Prefab structural panel crashes with entry door
Although it takes longer time and effort in the design, it is definitely worth doing because everyone will know what they are expecting to see when the project is completed.
By practicing detail design and construction plannings, we can avoid many mistakes in the constructions for example:

Wrong framing leads to stud crash with holddown bolt.

A design omission causes an additional bulkhead to hide HVAC ducts
Lastly, plan ahead helps the owner define the energy goals that will guide them to think about life cycle cost or total ownership cost instead of focusing on construction cost.
2. A more predictable construction schedule.
Delay is frustrating and stressful to most house owners, especially those who carry construction loans. Because we move structure or whole house construction into a controlled, enclosed environment, any weather will be less likely to affect the construction progress. We know when we will get the parts or house delivered, and we can prepare for what work we need to do.

After a heavy windy night…
These two attributes could lead to cost savings (Yes! you can save money from prefab if done right), energy savings, peace of mind, high quality, and many other good outcomes for landowners and developers.
In the next post, I will dive in with one of most unique prefab construction — modular system, to discuss its advantages and disadvantages.
Like some other equipment or programming, Fire TV Stick is inclined to glitches and breakdowns. What's more, when that occurs, one should show restraint for the vast majority of the things can be fixed with straightforward arrangements. Once in a while, when we lose the first frill or are only lethargic to interface them, we utilize an alternate USB link or connector for Fire TV. Assuming that your firestick keeps restarting all of a sudden, take a stab at stopping its unique extras.