The Facts of Going Modular
- TechPrefab
- Mar 16, 2021
- 6 min read
Modular is an exciting concept — to build a portion or whole building, from top to bottom, in a factory so that the onsite labor is reduced to lego-like block building. This is a very sexy idea because:
Off-site construction: The factory production model reduces safety risks. With volumetric production, higher quality control, and weather independence, the boxes can be built at a lower cost and a more predictable timeline.
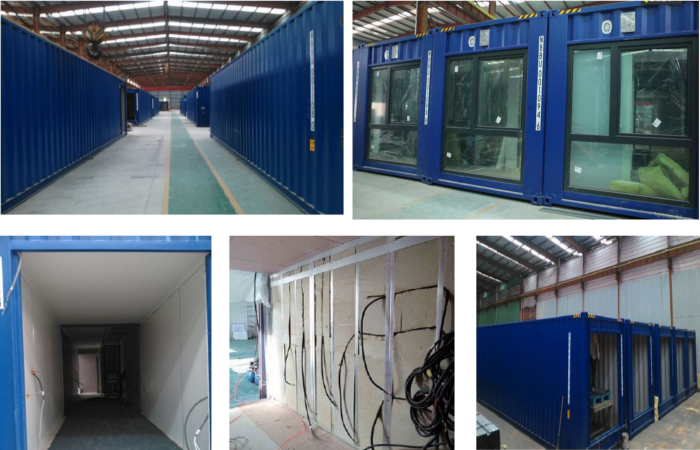
Tech Prefab factory partner student apartment project
2. On-site construction: The lego-like block stacking is an efficient and crazy fast construction method. You will see a mid-rise apartment rise in just days.

Crown plaza at Changi Airport, Singapore, Photo credit: Prefabmarket.com
3. Build Fast: Anyone who follows modular construction will know this modular schedule from the Modular Building Institute. One amazing attribute of prefab constructions is to parallelize the traditionally sequential work process to save a significant amount of time.

Modular Construction Schedule — Picture Credit: Modular Building Institute.
Besides the above mentioned, many modular factories also promote that build in a factory is greener, safer, with higher quality.
Are all these claims true? It depends. Let’s break the whole process into steps to see what you need to know before jumping into modular construction.
Design
To save money and time from modular, we have to start from the beginning. The best time to engage with a modular factory is at the planning stage. Although many modular professions claim the possibility of modular design is countless, the reality is, we need to prepare the design for doing modular.
To give an example, here is the case I worked on previously:
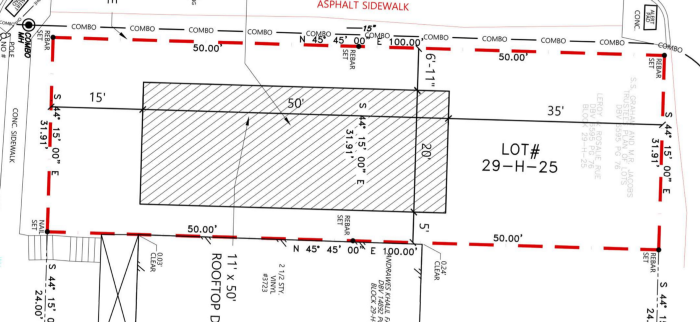
A city lot that is approved for a construction envelope of 20'x50'
The image shows a corner lot approved for side setback variance from the City. So the total buildable envelope is 20'x50' with 40' height constraints. Theoretically, the lot can have a three-story house with a total floor area of 3,000 sq.ft.
When planning for modular, we face a dilemma: most modular manufacturers build modular sizes in a few standard widths, typically 12', 13' or 13' 9 inches. Some companies also build width of 14'9" and 15'9". In this situation, using one module (15'9") per floor, the client lost at a minimum of 600 sq.ft. floor area, and using two modules per floor will increase the cost because it requires a custom module width.

A customized home floor layout using modular dimension — Tech Prefab.
The floor plan above is a good design or cost-saving design, and we have developed previously. The kitchen width is 11'5", which is narrow. Also, the double interior walls are called mating walls where shows the joint of the two boxes. The mating wall is recommended to preserve as much as possible.
Manufacturing
Many people think the module manufacturer could finish the entire box in the factory, so the on-site job is stacking them one on another. But there are still loads of work that have to be done on-site.
Every factory has its own set of material lists, which means that the client has to be responsible for delivering the products to the factory on time for any products that are not on the factory offering. The factory is usually located in rural areas, so shipping products such as windows and glass doors aren’t cheap.
Also, many products cannot be installed in the module for transportation safety — for example, wood flooring, countertop, and exterior finishes other than vinyl sidings. If your site is far away from the factory, a seasoned modular expert will also suggest you not to install heavy windows or doors in case of cracks on those materials. All these will increase the load of your site work once the modules are set.
Deliver date
Once we considered every aspect and accept all the modular specs, the next hurdle is on the module set date. The cost for the set heavily depends on how the site looks like. A challenging case could look like the one below. In the simulation, the crane has to be ready on site before the module comes. The crane is 75t with a max radius of 65'. The price is $465/standard hour, $615 per overtime hour, and the work has to be charged by 4,6,8 hours. The clock starts ticking when the crane left the garage, and we have to book the crane a week earlier. On the other side, the truck driver informed the project team that the module would be delivered in the morning, someday next week, with no specific time. Lastly, it would be best to get the set crew ready on site for utility hookup once the module is landed on the foundation. So, you need to precisely get three groups of people on-site for the big day — that is a lot of management!

Set module to the backyard.
A clearer way is to stock the modules to some places nearer to the site and then arrange for crane and set crews later. Module housing posted a nice video to show how this can be done.
Once the house is set, what left inside and outside the house should be picked up by the on-site general contractor to finish — this could include fixing the broken studs from the long hauling trip and installing exterior sidings, floorings, MEP systems, stairs (yes, no stair can be installed!) countertops…. It basically means another 4–8 weeks are needed to finishing up the project.
Furthermore, more facts about modular homes and their false claimed benefits:
A modular home may not as green as you think. First, to make the module withstand the loads from transportation, the factory uses more materials to enhance its overall structures. Second, recycle material scrape is definitely a false claim. The factory is getting the same 4x8 boards, 2x6 studs. Any scrapes will be expensive to recycle. Third, transportation could cause damages to the studs and doors — thus cause on-site material replacement.
Modular homes aren’t 100% faster than traditional construction. Many factories have more than 8 weeks of back-logs. It means you have to spend at least 12 weeks (4 months!) to get a modular home assuming you already have permit approval. The timeline is rather similar to the national home builder’s 5–6 months from design to finish.
Modular homes aren’t cheaper. In my previous blog, I posted one example of the modular factory’s offering — it is comparable to the local stick-built quote, but not cheaper. People often ignore the factory overhead and profit, transportations, and crane costs added for a home project.
Modular is more energy efficient? I also doubt this claim because most of the modular factories are using the same material as stick-built. 2x6 wood frame, R19 insulation, double glazing layer, and building code (IRC)… I also couldn’t find any evidence show modular houses are tighter than stick-build, though I expect stick-built houses do have larger uncertainties on airtightness.
The modular industry is still facing many challenges in the market, and the limitations of transportation have disqualified it from many projects. But, its advantages are also much superior to all the other construction methods.
The speed of onsite construction: The quality has made modular construction attractive for many medium-large projects inside the city. In a metropolitan area, such as NYC or Singapore, the speed of onsite construction means everything. For example, over 200 modules on the crown plaza were set in 26 days, with no interruption to the daily airport business.
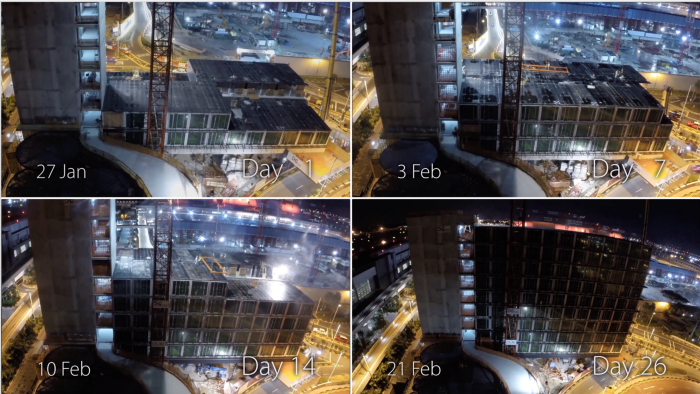
Crown Plaza at Changi Airport — Time Elapse Video (Credit to Unitised Building)
2. Factory production: When doing the same module in volume, the factory overhead per capita drops significantly, and so does the crane cost. This means to gain the most cost-saving potential from modular. We have to buy a volumetric design off the shelf from a factory or develop hotels, apartments, and hospitals designed to be modular friendly.
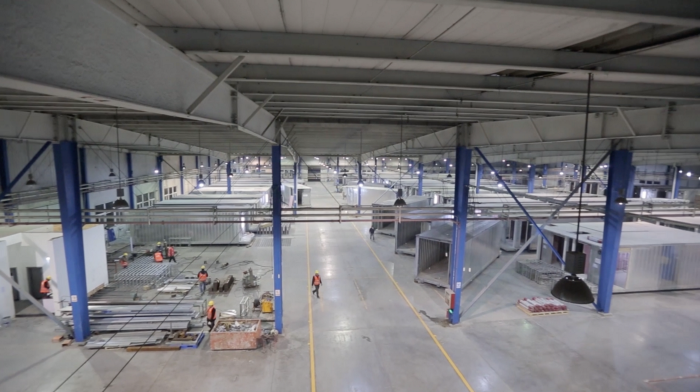
Unitised Building Container Modular Factory
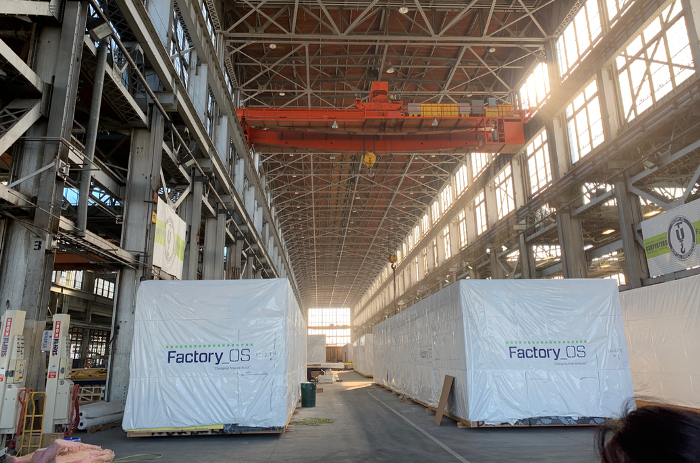
Factory OS production line — ready for shipment
There are still many interesting ideas around the modular, for example, container houses, the differences between modular and manufactured homes, etc. I will cover most of the topics in my follow up blogs.
In summary, modular is an innovative technology rather than disruptive. The best application is for projects that contain repetitive floor layouts and time-limited on-site construction. However, we do see other trends become pretty interesting. For example, using 3D printing to automate the module build in the factory (Mighty Building). We will see more incremental innovations happen in the industry and eventually become disruptive.
Comentários